Here is a list of frequently asked questions we often receive. If your questions are not addressed in this section, do not hesitate to contact AIC directly for further assistance.
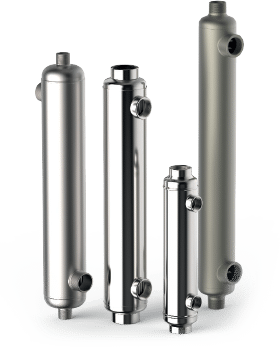
Certifications
What does ASME stand for, and do I need it for my installation? How does it differ from UL?
Local plumbing codes and legislations will often dictate what certifications are required. Although the majority of institutional, commercial, and industrial installations do require some form of certification, it also depends on the size of the unit, what the heat exchanger is designed to do, and the specific market you’re in.
What is C.R.N. and do AIC products contain the C.R.N number?
The Canadian Registration Number (C.R.N.) is a number issued by the technical safety authority in the individual Canadian provinces identifying the product design as being accepted and registered for use in that province. Many of AIC’s standard heat exchangers do have CRN registration for use across Canada.
Product Selection
What information do I need to select and size a heat exchanger?
Proper understanding, and actively maintaining and controlling the temperature, flow, and pressure inputs into the heat exchanger, and defining its outputs – exit temperatures, BTU requirements- will assist in the overall sizing of the heat exchanger. Selection of a product that is either undersized or too oversized may lower the heat transfer effectiveness of the unit.
As a minimum, five parameters are required to properly size a heat exchanger:
- operating flow rates for the hot and/or cold side
- inlet temperatures of the hot and/or cold side
- outlet/exit temperatures of the hot and/or cold side
- total heat load
Ensure that the operating fluids are specified in order to determine their behaviour.
How do I know if I need a plate or tubular heat exchanger?
Application parameters will typically dictate which design is more effective for the job. Here are a few variables to consider:
Fluid Flow and Pressure Drops: A tubular type of heat exchanger (removable u-tube, straight tube, or welded shell & tube design) will generally allow for larger amounts of fluid through the unit with relatively lower pressure drops than when compared to a plate exchanger (brazed plate or plate & frame), whose dense plate packs acts as a restriction barrier.
Heat Transfer Area: Due to the thin plates and chevron designs of their tight plate packs, plate heat exchangers have a high heat transfer rate to surface area ratio, meaning that these exchangers may be more favourable for applications with lower temperature differentials or when a close temperature approach is required. For plate & frame heat exchangers, if the frame allows for it, additional plates may be added on to an existing unit, on site, to increase the heating surface area.
Hardiness: Industries such as oil & gas prefer the use of tubular heat exchangers for the ruggedness and flexibility of the design. Thick tubes and shells. Use of expansion joints. Resilience with different fluid types – viscous oils, steam, etc. There is wider scope in tubular designs than compared to plate designs, enabling more customization of the product to suit a client’s particular needs.
Maintenance: Both plate and tubular designs carry products that are either ‘removable’ or ‘welded/brazed’. Plate packs in plate & frame exchangers may be removed, cleaned, and/or replaced. Tube bundles in u-tube or straight tube heat exchangers may be removed, cleaned, and/or replaced. One may argue that it is a more arduous task in one design than the other; however, that is up to the client to determine.
Certifications: If required, both plate and tubular heat exchangers may be designed to the ASME Code. Tubular exchangers may also be governed by TEMA standards.
Why can’t I use stainless steel heat exchangers for salt water pool applications?
For such demanding applications, AIC offers products with materials available in titanium and marine-grade, super austenitic alloys.
Do I need a single wall, or a double wall, heat exchanger to use with potable water?
Note that standard AIC double wall heat exchangers are not certified to be use in lethal service, and should not be exposed to chemicals corrosive to the products, compromising the effectiveness of the double wall design. Should the products be used with fluid(s) that may be irritating or harmful to the body in any way, the user is responsible to ensure that all safety precautions are taken in the design and maintenance of the system.
Can I use brazed plate heat exchangers for steam applications?
It is not recommended to use brazed plate heat exchangers in steam applications. The rigid structure of the brazed plate pack will be susceptible to failure (leaks and physical deformation) when exposed to any expansion/contraction associated with steam phase changes.
Operations
Do I need to clean my heat exchanger?
In short, yes. A proper maintenance program ensures longevity and effectiveness of the heat exchanger, by freeing the unit of debris buildup that may hinder its performance and potentially propagate structural damages. Routine inspections will also help to identify, early on, any concerns with the product and to mitigate the issues.
How do I connect my heat exchanger to the system?
Installation information is found in the operating manual that accompanies each product. If one is not available, please contact AIC for assistance. Typically heat exchangers are the most effective when connected in a counterflow configuration – that is, the hot side inlet adjacent to the cold side outlet. This may differ, however, depending on the geometry of the heat exchanger and your specific application.
How do I determine the maximum allowable flow rate through my heat exchanger?
The maximum flow through a heat exchanger is dictated by the size of the connections, the number of plates (in plate products) or number/length of tubes (in tubular products), and the client’s pressure drop requirements. Please consult AIC’s technical specifications for approximate values.
Are gaskets glued to the plates in plate & frame heat exchangers?
All plate and frame heat exchangers supplied by AIC have glueless gaskets, and can be easily removed and replaced.
Can I connect steam through the bottom inlet of my heat exchanger?
It is recommended that steam enters through the top connection. Due to the nature of steam, if it is connected to the bottom of the heat exchanger, the steam will condense as it rises through the unit. The condensate will flow downwards, because of gravity, and hinder the flow of the incoming steam.